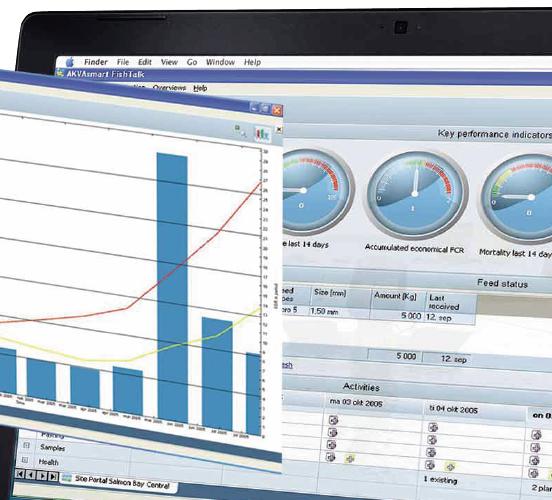
Technology can relieve the increasing pressure on job shops, machine shops and make-to-order manufacturers, but choosing the right system is the major imperative, says Thomas R. Cutler.
Greg Ehemann and Rich Ehemann, Shoptech’s founding partners, have been around job shops their entire careers. While working in a machine shop in Cincinnati, Ohio during the 1980s, Greg and his brother Rich were frustrated that they could not determine whether they were making or losing money on a job.
Out of that frustration, the two brothers collaborated to develop a computer system to track actual costs and monitor profitability. They also experienced firsthand the need for better coordination of the other facets of running a job shop: estimating, scheduling, collecting time from the shop floor, purchasing, shipping, and even accounting.
Out of their experience with shops and their passion for computers came a software product and a company that was built from the ground up, a real success story. Today, Greg and Rich Ehemann (the two Es of the E2 Shop System) are still involved in the day-to-day operations of the business. Their passion is evident as the E2 Shop System now has thousands of customers and five offices across North America.
There are many reasons why technology implementations fail in a job shop environment. Lack of management commitment, inadequate education and training, poor planning, not enough resources, to name just a few, but there is a more basic reason—choosing the wrong system.
Whether a job shop, machine shop, or make-to-order manufacturer, there are similar problems shared. Companies face increasing pressures from customers, dealing with constant change, meeting customers’ due dates, and scheduling the shop floor.
Companies look to information technology to help improve processes and gain a competitive edge. Most systems have a heritage in the material requirements planning (MRP) philosophy developed more than forty years ago. Utilizing computer power to calculate time-phased material requirements this later evolved into MRPII, promoted by APICS and Oliver Wight during the 1980s, and further evolved to the enterprise resource planning (ERP) systems available today.
The original premise of these systems was that material planning is the center of the universe. The typical manufacturing system was designed with an MRP process at the heart of the system. The emphasis was on standard bills and routings and standard costs.
Job shops, machine shops, or make-to-order manufacturers have a different focus. To win business, they must provide accurate estimates and quotations to a demanding customer base. In many cases, bills and routings are specific to a job and you must closely monitor actual costs versus the original estimate to ensure profitability.
All software vendors say their product is easy to use; within a few minutes of a demo, users should be able to understand how the system would work in a real world environment. If the product is not easy to use then training will be more difficult and time-consuming. Employees are more likely to make mistakes. Overall implementation time will be longer and reaping the benefits of the new system will take a long time. More important than the speed of implementation, is on-going use. Employees quickly stop using a system that is a hindrance rather than a help.
Estimates and quotation management for job shops
It all starts with the estimate. The ability to estimate potential costs and to determine a fair selling price can make the difference between winning business and winning profitable business. Creating a one-off detailed estimate can be very time-consuming, considering that the data may reveal it is best not to bid at all.
When time is of the essence, a job shop’s first estimate may be a rolled up summary of large buckets of labor/machine hours or material dollars. Often job shops copy an estimate from a similar job and make adjustments accordingly. Some companies have custom-built applications using such tools as spreadsheets or Microsoft Access to create estimates. These applications may contain specific logic, which is unique to a company and it must be retained.
Scheduling and shop management
When a customer calls and wants to know the status of their job(s), the information must be instantly available without having to go on the shop floor. Many companies are familiar with the manual visual scheduling tools such as cards, magnetic colored strips, or just writing on a whiteboard. Today, shop management software provides the same visual benefits of a scheduling board on the PC.
There are many different techniques for shop scheduling including forward/backward, finite/infinite including user defined “tie breakers” when multiple jobs are competing for the same resource. Another important feature is the “what-if” simulation that allows management to answer customer requests for promise dates. Job shops must have the option of selecting the best methodology.
Viewing job status is only useful if the data collected on the shop floor is up-to-date and accurate. Getting up-to-date job tracking and costing information and ensuring that time is booked to the correct job, shop floor data collection equipment is an important addition to any system.
The system selected should be flexible, allowing for multiple shop floor data collection methods, from manual timecards to data collection devices, scanners, and touch screens on a PC. Many shops want to move towards a paperless shop floor by allowing workers to view all the information they need on a computer screen instead of paper such as a list of all jobs scheduled on work centers, work instructions, CAD drawings and images.
Quality management in job shops includes ISO
Customers expect products manufactured to specification and delivered on time. With so much competition for every job coupled with slim margins, no manufacturer can afford to spend time and money on rework. An integrated quality system allows job shops to easily collect and analyze data to identify production problems earlier in the production process, thereby reducing rework, returns, and customer complaints.
Today, many companies require suppliers to be ISO 9001 certified. The amount of time required to pass an audit and achieve certification is significant. One of the most time-consuming aspects of certification is documenting business processes. A job shop system forms the framework from which business operates and is an integral part of the ISO 9001 certification process.
If the system contains pre-defined templates of each business process, then this can go a long way helping to create the necessary documentation required for certification. Few technology solutions providers include the quality module as part of the core system, rather offering a third-party addition. The system should automatically collect all quality data and schedule and track all preventive maintenance; help identify and control potential problems before they affect due dates or quality ratings. Ideally, the solution should help create quality documents for ISO 9000 certification
Shoptech’s E2 founders, Greg Ehemann and Rich Ehemann insist, “While large companies can absorb the cost of a failed implementation, small companies can be devastated by the wrong choice. Most job shops, machine shops, or make-to-order manufacturers are small, privately owned business, so it is essential that they make the right choice, the first time. Taking the time to focus on the things that matter ensures the best possible technology solution.” http://www.shoptech.com
* * *
Thomas R. Cutler is president & CEO of Fort Lauderdale, Florida-based, TR Cutler, Inc, (www.trcutlerinc.com). Cutler is the founder of the Manufacturing Media Consortium of nearly four thousand journalists and editors writing about trends in manufacturing. Cutler is a member of the Society of Professional Journalists, Online News Association, American Society of Business Publication Editors, Committee of Concerned Journalists, as well as author of more than 500 feature articles annually regarding the manufacturing sector. Cutler can be contacted at trcutler@trcutlerinc.com or 888-902-0300.